Compliant mechanism
In mechanical engineering, a compliant mechanism is a flexible mechanism that achieves force and motion transmission through elastic body deformation.[1] It gains some or all of its motion from the relative flexibility of its members rather than from rigid-body joints alone. These may be monolithic (single-piece) or jointless structures.[2] Some common devices that use compliant mechanisms are backpack latches, paper clips, and nail clippers. One of the oldest examples of using compliant structures is the Bow and arrow.[3]
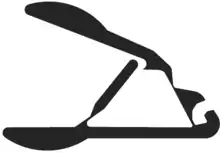
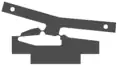
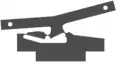
Design methods
Compliant mechanisms are usually designed using two techniques:[4]
Kinematics approach
Kinematic analysis can be used to design a compliant mechanism by creating a pseudo-rigid-body model of the mechanism.[3] In this model, flexible segments are modeled as rigid links connected to revolute joints with torsional springs. Other structures can be modeled as a combination of rigid links, springs, and dampers.[2][5][6]
Structural optimization approach
In this method, computational methods are used for topology optimization of the structure. Expected loading and desired motion and force transmission is inputted and the system is optimized for weight, accuracy, and minimum stresses. More advanced methods first optimize the underlying linkage configuration and then optimize the topology around that configuration.[2] Other optimization techniques focus topology optimization of the flexure joints by taking as input a rigid mechanism and replacing all the rigid joints with optimized flexure joints.[6] To predict the behavior of the structure, finite-element stress analysis is done to find deformation and stresses over the entire structure.
Other techniques are being conceived to design these mechanisms. Compliant mechanisms manufactured in a plane that have motion emerging from said plane are known as lamina emergent mechanisms (LEMs).
Advantages
Compliant structures are often created as an alternative to similar mechanisms that use multiple parts. There are two main advantages for using compliant mechanisms:
- Low cost: A compliant mechanism can usually be fabricated into a single structure, which is a dramatic simplification in the number of required parts.[2] A single-piece compliant structure can be manufactured through injection molding, extrusion, and 3d printing, among other methods. This makes the manufacturing relatively cheap and accessible.[2][3]
- Better efficiency: Compliant mechanisms do not suffer from some issues that affect multi-bodied mechanisms, such as backlash or surface wear. Due to the usage of flexible elements, compliant mechanisms can easily store energy to be released at a later time or transformed into other forms of energy.[3]
Disadvantages
The full range of a mechanism depends on the material and geometry of the structure; due to the nature of flexure joints, no purely compliant mechanism can achieve continuous motion such as a normal joint. Also, the forces applied by the mechanism are limited to the loads the structural elements can withstand without failure. Due to the shape of flexure joints, they tend to be locations of stress concentration. This, combined with the fact that mechanisms tend to perform cyclic or periodic motion, can cause fatigue and eventual failure of the structure. Also, since some or all of the input energy is stored in the structure for some time, not all of this energy is released back as desired. However, this can be a desirable property to add damping to the system.[3]
Applications
Some of the oldest uses of compliant structures date back to several millennia. One of the oldest examples is the bow and arrow. Some designs of catapults also made use of the flexibility of the arm to store and release energy to launch the projectile larger distances.[3] Currently, compliant mechanisms are used in a variety of fields such as adaptive structures and biomedical devices. Compliant mechanisms can be used to create self-adaptive mechanisms, commonly used for grasping in robotics.[7] Since robots require high accuracy and have limited range, there has been extensive research in compliant robot mechanisms. Microelectromechanical systems (MEMS) are one of the main applications of compliant mechanisms. MEMS benefit from the lack of required assembly and simple planar shape of the structure which can be easily manufactured using Photolithography.[2]
The flexible drive or resilient drive, often used to couple an electric motor to a machine (for example, a pump), is one example. The drive consists of a rubber "spider" sandwiched between two metal dogs. One dog is fixed to the motor shaft and the other to the pump shaft. The flexibility of the rubber part compensates for any slight misalignment between the motor and the pump. See rag joint and giubo.
Research laboratories and researchers
A number of labs and researchers are explicitly researching compliant mechanisms:
- Prof. Larry Howell, Brigham Young University Compliant Mechanisms research[1]
- Prof. Haijun Su at the Ohio State University[8][9]
- Dr. Shane Johnson at the University of Michigan Joint Institute, SJTU, Shanghai.
- Prof. Kota at University of Michigan Compliant Systems Design Lab[10]
- Prof. Zentner at Ilmenau University of Technology[11]
- Prof. Martin Culpepper at MIT Precision Compliant Systems Laboratory[12]
- Prof. Just L. Herder at Delft University of Technology[13]
- Prof. Engin Tanık and Prof. Volkan Parlaktaş at Hacettepe University[14]
- Prof. Jonathan Hopkins at University of California, Los Angeles[15]
- Prof. Dannis Brouwer at the University of Twente, The Netherlands[16]
- Prof. Alexander Hasse at Chemnitz University of Technology[17]
- Prof. Jared Butler, The Pennsylvania State University, University Park
In addition, the following researchers may be doing compliant mechanism research:
- The Multidisciplinary and Multiscale Device and Design Laboratory (M2D2) at the Indian Institute of Science, Bangalore[18]
- Prof. Sridhar Kota[19]
- Prof. Shorya Awtar at University of Michigan[20]
- Prof. G. K. Ananthasuresh at IISc, Bangalore[21]
- Prof. Stephen L. Canfield at Tennessee Tech University[22]
- Prof. Charles Kim at Bucknell University[23]
- Prof. Anupam Saxena at IIT Kanpur, India[24]
- Prof. Mary Frecker at The Pennsylvania State University, University Park[25]
- Prof. Guimin Chen, Compliant Mechanisms and Its Applications at Xi'an Jiaotong University[26]
- Prof. Guangbo Hao, Compliant Mechanisms and Robotics Research Group at University College Cork, Ireland[27]
- Prof. W.J. Zhang, Soft Body Mechanisms and Robots Research Group at University of Saskatchewan, Canada[28]
- Prof. Stuart Smith, Instrumentation development group, University of North Carolina at Charlotte, USA [29]
Image Gallery
- A laser welding robot positions the workpieces by a compliant mechanism between table and fixture
- Compliant Iris mechanism - closed
- Compliant Iris mechanism - open
- Compliant clip
- Bistable compliant switch mechanism
References
- "CMR Awarded Research Grant from National Science Foundation". Cmr.byu.edu. Retrieved 21 February 2015.
- Perai, Seberang. "Methodology of compliant mechanisms and its current developments in applications: a review." American Journal of Applied Sciences 4.3 (2007): 160-167.
- Howell, Larry L. "Compliant mechanisms." 21st Century Kinematics. Springer, London, 2013. 189-216.
- Alejandro E. Albanesi, Victor D. Fachinotti and Martin A. Pucheta: [www.cimec.org.ar/ojs/index.php/mc/article/viewFile/3015/2946%7Cdate=October A review of design methods for compliant mechnasms.] In: Mecánica Computacional, Vol XXIX, pages 59-72. Eduardo Dvorkin, Marcela Goldschmit, Mario Storti (Eds.) Buenos Aires, Argentina, 15-18 November 2010.
- Albanesi, Alejandro E., Victor D. Fachinotti, and Martin A. Pucheta. "A review on design methods for compliant mechanisms." Mecánica Computacional 29.3 (2010).
- Vittorio Megaro, Jonas Zehnder, Moritz Bächer, Stelian Coros, Markus Gross, and Bernhard Thomaszewski. 2017. A Computational Design Tool for Compliant Mechanisms. ACM Trans. Graph. 36, 4, Article 82 (July 2017), 12 pages. https://doi.org/http://dx.doi.org/10.1145/3072959.3073636
- Doria, Mario; Birglen, Lionel (2009-03-17). "Design of an Underactuated Compliant Gripper for Surgery Using Nitinol". Journal of Medical Devices. 3 (1): 011007–011007–7. doi:10.1115/1.3089249. ISSN 1932-6181.
- "Home Page - DAS 2D/3D". DAS 2D/3D. Retrieved 2015-11-11.
- "Design Innovation and Simulation Laboratory". Design Innovation and Simulation Laboratory. Retrieved 2015-11-11.
- "U of M - Compliant Systems Design Laboratory". Sitemaker.umich.edu. Archived from the original on 2014-05-06. Retrieved 2015-02-21.
- "FG Nachgiebige Systeme". www.tu-ilmenau.de (in German). Retrieved 2017-08-03.
- "MIT Precision Compliant Systems Laboratory Home". Pcsl.mit.edu. Archived from the original on 2012-12-14. Retrieved 2015-02-21.
- Archived November 16, 2012, at the Wayback Machine
- "CRMR". Yunus.hacettepe.edu.tr. Retrieved 2015-02-21.
- "Flexible Research Group". ucla.edu. Retrieved 2017-12-02.
- "Precision Engineering". utwente.nl. Retrieved 2018-11-26.
- "Nachgiebige Systeme". www.tu-chemnitz.de/mb/mp/ (in German). Retrieved 2018-05-22.
- "M2D2 Index". Mecheng.iisc.ernet.in. Archived from the original on 2015-02-21. Retrieved 2015-02-21.
- "Sridhar Kota | me.engin.umich.edu". Personal.umich.edu. Retrieved 2015-02-21.
- "Precision Systems Design Lab". Personal.umich.edu. Retrieved 2015-02-21.
- "Ananthasuresh". Mecheng.iisc.ernet.in. Archived from the original on 2015-02-21. Retrieved 2015-02-21.
- "Stephen L Canfield, Ph.D., Professor of Mechanical Engineering". Archived from the original on November 20, 2012. Retrieved July 15, 2013.
- "Mechanical Engineering Department: Charles J. Kim". Archived from the original on May 13, 2008. Retrieved May 9, 2008.
- "index_iitk_32". Home.iitk.ac.in. Retrieved 2015-02-21.
- "Home". Edog.mne.psu.edu. Archived from the original on 2015-02-16. Retrieved 2015-02-21.
- "Compliant Mechanisms & Precision Instruments". web.xidian.edu.cn. Retrieved 2015-05-06.
- https://sites.google.com/site/doctorghao/
- https://homepage.usask.ca/~wjz485/
External links
- Why Machines That Bend Are Better – YouTube video by Veritasium
- - YouTube video - A Computational Design Tool for Compliant Mechanisms by Disney Research Hub
- - BYU Compliant Mechanisms Research